Optimisation of roughing and finishing with milling of special materials
To identify the causes of premature wear of the tool, enhance cutting conditions and simulate the required power.
The reduction of wear in percentages equal to or greater than 60%.
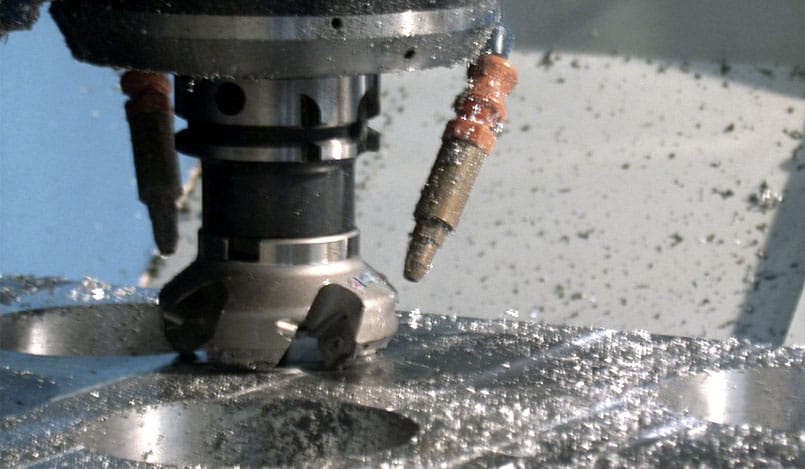
The customer had already tested various geometries and qualities of tools for mill roughing of special steel alloys. However, the hardest cutting plates fracture and the toughest ones suffer premature wear.
Laboratory analysis of samples clearly revealed wear from adhesion. The material welds to the plate and gradually fractures. Unlike what was expected fromusing low cutting speeds, this adhesion was due to the poor advance of the cutting tooth, preventing the correct flow of material. With three times greater feed or tool advance conditions the adhesion of the material was eliminated satisfactorily, reducing the rate of wear by 60%.
The finishing operation, on the other hand, shows thermomechanical fissures. The customer was not prepared to reduce the diameter of the tool, given that this would have meant less productivity. The cutting speed was reduced and, at the same time, the number of cutting teeth increased, obtaining 75% less wear.