Towards metrology that is automated and integrated in production
All the progress made in terms of digitisation and automation has given rise to unprecedented levels of technological development as regards fitting robots, machines and processes with measuring instruments and advanced use procedures.
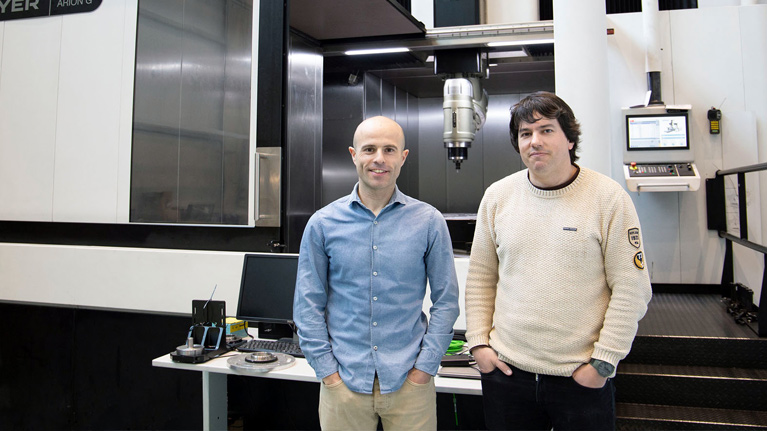
Authors: Unai Mutilba and Gorka Kortaberria, researchers of the Precision and Metrology Group at Tekniker
Metrology and integrated sensorics have made it possible to perform real-time monitoring of machines and processes; data can be obtained instantaneously, and control and traceability can be achieved throughout the entire life cycle of a product from the moment of its inception and until it is applied in a real environment.
Thanks to the digitisation of production processes, metrology is no longer considered to be the last link in an industrial process but rather an optimum ally that allows advanced manufacturing to address all the challenges posed by a smart industry model.
The transition is speeding up under the influence exerted by production demands in some of the most relevant industrial sectors: automation and aeronautics.
In the Basque Country, most of the progress made in the area of fundamental research related to precision engineering and metrology to meet these needs is being addressed by the research group featuring Tekniker working in close cooperation with Ideko, Tecnalia, Vicomtech, the University of the Basque Country (UPV/EHU) and IMH Campus.
But what are the main challenges associated with performing metrology activities in a non-controlled digital environment in the case of production resources or processes?
Uncertainty and traceability
In order to understand the significance of this challenge, it would be first necessary to focus on two of metrology’s main properties: the allocation of measurement uncertainty and how metrological traceability can be guaranteed.
Measurement uncertainty is technically defined as a “non-negative parameter that characterises the values allocated to a measurand” and allows you to discover the extent of an error whenever measurement outcomes are reported.
As regards metrological traceability, the term refers to “the property by means of which the outcome of a measurement can be related to a reference measurement by means of an uninterrupted and documented chain of calibrations”.
Both properties are relatively well controlled whenever metrology is performed in a laboratory setting in a controlled environment, although the same does not apply when this happens in a production environment.
In the case of measurement uncertainties associated with a machine and a process, our challenge consists in minimising them at a reasonable economic cost and, what is even more important, performing quantifications.
Production environments are characterised by a number of variables that constrain metrology during a process due to elements such as temperature, the presence of vibrations or soiling in certain manufacturing processes.
A number of requirements must also be met with regard to response times and there has to be a sufficient level of accuracy to incorporate metrology as an active element in manufacturing processes.
An unprecedented technological development
An unprecedented technological development has been carried out to properly address this challenge and integrate advanced use procedures and measurement instruments in resources and processes.
For instance, new sensors are currently being developed to monitor production processes; processing and measurement procedures are being automated by means of instruments installed on industrial robots and machine tools can be used to perform contact/contactless metrology.
Download the paper in full.