Surface treatments for environmental sustainability
The ultimate goal of the European BIOFIRE project is to use surface treatments in order to double the operating life of biomass boilers. In particular, the role played by Tekniker in this initiative consists in developing test protocols to simulate the behaviours of new surface treatments under conditions that are as similar as possible to real operating conditions.
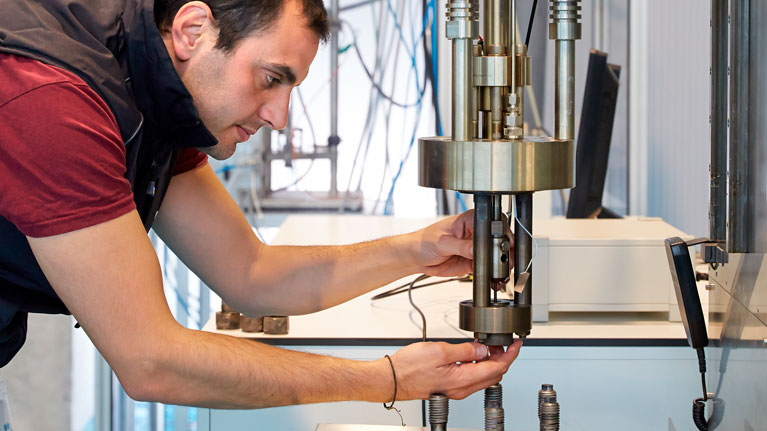
Traditionally, coal has been used for large-scale energy generation. Fossil fuels of this kind and other similar alternatives, however, are gradually being replaced by biomass as a source of energy for boilers or burners and they are frequently combined with coal to reduce the latter’s environmental impact. The need to reduce CO2 emissions and, consequently, greenhouse effects, poses new challenges for boiler materials as the use of these new fuels significantly increases the risk of developing severe corrosion and erosion affecting the pipes where the steam produced by boilers circulates.
Consequently, the European BIOFIRE project has been set into motion to develop new surface treatments that can double the operating life of biomass boilers. A project in which Tekniker, member of the Basque Research and Technology Alliance (BRTA), will be playing an outstanding role thanks to its specialisation in tribology.
In this regard, the technology centre boasts a track record of nearly 40 years of experience in the area of tribology. Over the years, the organisation has acquired extensive knowledge with regard to friction mechanisms, mechanical wear, chemical wear (corrosion) and wear-corrosion synergies at different scales (nano-macro) and also with regard to simulating and modelling by means of laboratory tests and mathematical calculations. In this way, it becomes possible improve the quality and durability of surfaces in contact with real components and also study their compatibility and interactions with the environment.
More specifically, the role played by Tekniker consists in developing new experimental laboratory protocols to simulate corrosion, erosion and thermal-mechanical stresses that new surface treatments will be exposed to in order to assess performance and select the most promising alternatives. Consequently, it will be possible to validate the most suitable solutions before other partners running real plants test the resulting coated pipes.
Developing new diffusion surface treatments
New diffusion surface treatments will be developed within the framework of this project applied by means of the “Pack Cementation” and “Slurry” techniques used on internal and external pipe surfaces. As these surface treatments will be incorporated to the production processes, major innovations will occur at an industrial level because, so far, this takes place in different processes.
The main advantages resulting from coating these pipes show that their degree of resistance to corrosion and environmental erosion is enhanced and this extends their operating life, although the goal set by the project is aimed at doubling operating life for pipes. It will also still be possible to use the same reference steel grades currently available on the market as it is a well-known fact that these grades meet all weldability and conformability requirements of this application. This means, therefore, that it will not be necessary use other more expensive types of steel that do not meet these requirements or pose difficulties when used.
In addition applying this technique to pipes fitted on biomass burners, it will also be possible to use the technologies developed by Tekniker with regard to coatings and test protocols in other high-temperature applications exposed to highly corrosive environments such as turbines, furnaces or heat exchangers.
Thanks to a single production process it will be possible to extend the life of burner pipes, to operate under more extreme conditions, avoid unscheduled shutdowns and reduce cleaning and maintenance costs in general. Accordingly, this will give rise to significant cost reductions and increase the competitiveness of a technology that is characterised by a low environmental impact.
BIOFIRE is a four-year European project under the RFCS (Research Fund for Coal and Steel) call in which companies and technology centres from the following 6 European countries are involved: Germany, Belgium, Spain, Hungary, Italy and Poland.