Precision in additive wire manufacturing processes
Tekniker coordinates the European project ASSALA, which aims to guarantee structural integrity in the process of manufacturing metallic components by this technique. Specifically, the technology centre is developing methods for predicting errors in the positioning of the robots responsible for the additive manufacturing by means of simulation models.
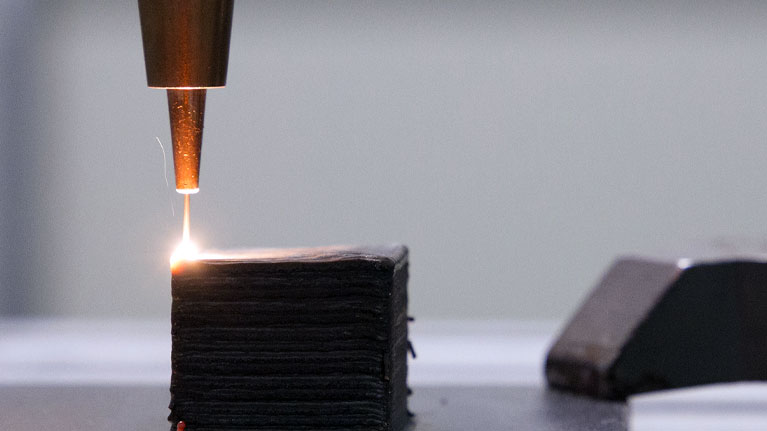
The technique of additive wire manufacturing using laser is one of the most promising technologies for producing large parts in sectors such as the aeronautical industry. It offers advantages such as a higher structural quality of the deposited material, thanks to lower levels of gas entrapment and pores. For this technique to be implemented optimally, high precision and robust structural integrity are required to guarantee "zero defect" products.
In this context, Tekniker, a member of the Basque Research and Technology Alliance (BRTA), is coordinating the European project ASSALA with the aim of predicting the probability of defects in metal components manufactured by means of additive wire manufacturing and thus guaranteeing structural integrity in the manufacturing process. Also participating in the project are the Swedish headquarters of GKN Aerospace and the French engineering school ENSAM Arts et Métiers.
Specifically, the technology centre is developing methods for predicting errors in the positioning of the robots responsible for additive manufacturing, as well as mitigation strategies through dynamic compensation models to increase their accuracy. To this end, Tekniker is focussing its research on two lines of work concentrating on the deposition of titanium by wire: the development of dynamic robot simulation models in order to validate their application to additive manufacturing and the improvement of dynamic compensation tools to increase their precision.
Therefore, Tekniker will develop dynamic precision improvement methodologies applicable to any robot-based additive manufacturing process, regardless of whether the material is in powder or wire form. In this way, possible errors in the positioning of robotic tools will be predicted and their application to this technique will be validated.
The technology centre has extensive experience in developing solutions for industrial robotics, high-precision metrological systems and laser supply for the manufacture of components.
Dynamic Robot Simulation Models
Until now, companies that made use of this technique, called LMD (Laser Metal Deposition), have faced a higher economic cost and the inconvenience of having to explore a large number of parameters, usually through a trial and error procedure, to ensure optimal results.
Unlike solutions currently on the market, the ASSALA model helps to achieve a more robust wire laser deposition process in terms of precision, speed and lower material costs. In this way, the use of a more economical machine robot architecture will improve the quality of the wire feeds and prevent the likelihood of failure of metal components.
During this development phase, the project has advanced in the implementation of kinematic simulation models of robots, verifying their initial state and improving their precision in static positioning, as well as in the numerical simulation of the material supply process used, by means of an application that enables the effect of the process parameters on the distortion of a typical component to be obtained in real time.
Likewise, within the framework of this project, optimisation algorithms will be developed based on the hybridisation of physics and data to ensure the correct selection of process parameters, accelerating calculation times without losing precision and providing information almost in real time. This application can also be extended to all types of additive manufacturing processes and metallic and non-metallic materials.
These robot and process models are integrated into a single framework (interface, software) and are used to manufacture standard components. In addition, these methodologies can be applied to any additive manufacturing process using robotic tools, regardless of whether the material is in powder or wire form, thus achieving results that ensure structural integrity in the manufacturing process.
This project has received funding from the Clean Sky 2 Joint Undertaking (JU) under grant agreement No 831857. The JU receives support from the European Union’s Horizon 2020 research and innovation programme and the Clean Sky 2 JU members other than the Union. This work reflects only the author´s view and the JU is not responsible for any use that may be made of the information it contains.