Plastic welding
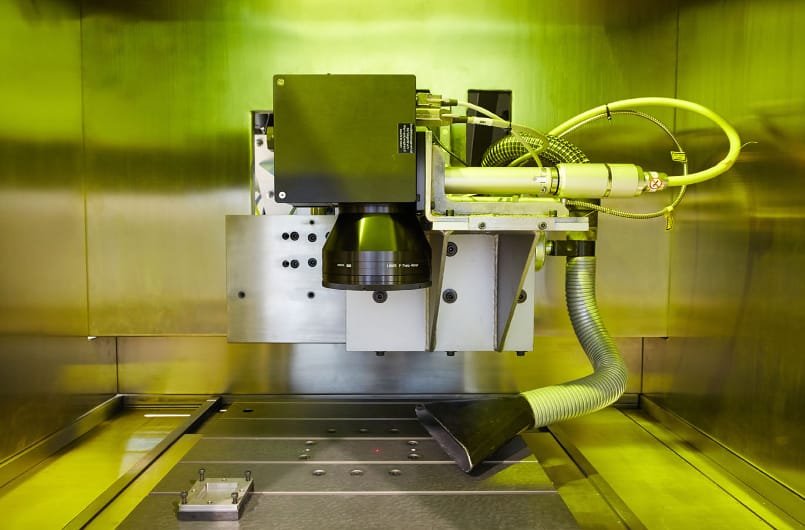
One of the processes of materials with laser which, in the past decade, has attracted particular interest amongst various industrial sectors (automobile, assembly and biomedicine), is thermoplastic welding. Compared to other, conventional techniques, (mechanical union or by using adhesives), thermoplastic welding using laser provides a wide range of advantages, such as high breaking strains, reducing processing times and minimising the thermally affected zones.
The welding of dissimilar materials has recently accrued special relevance. They usually have applications where the requirements involve reducing the weight of the structures (the automobile sector), substituting metal components with plastic ones through creating assemblies of dissimilar plastic-metal materials. These assemblies are undertaken using laser welding with a great variety of thermoplastics and metals.
TEKNIKER specialisation in the area of thermoplastic welding is focused on both the welding of similar materials (plastic-plastic) as on that of dissimilar ones (plastic-metal).
The most widely used technique in plastic-plastic laser weldingis by transmission. The viability of this process requires that the thermoplastic be absorbent to the laser radiation applied, while the other thermoplastic be transparent. During the welding process the laser beam pierces the transparent polymer, the energy of the laser being absorbed by the other thermoplastic, until its point of fusion. On this occurring, and thanks to a "perfect" contact between the polymers, guaranteed by suitable tools, the melted thermoplastic heats the transparent polymer, thus forming the union between the two.
In the case of plastic-metal laser welding the physical principle responsible for the union is different from the case of plastic-plastic welding. Firstly, it is important to point out that in this case there are no restrictions with regard to the optical properties of the plastics. The welding process can be carried out both for thermoplastics absorbent to the laser radiation as well as for transparent ones. In both cases the metal requires pre-treatment, also undertaken with laser. This pre-treatment involves generating cavities in the metal, in which the melted thermoplastic is inserted during the welding process. Thus, in this case, the principal mechanism for the union is mechanical.