ERLO Group and Tekniker join forces in Industry 4.0
The technology centre is currently cooperating with ERLO Group to develop the INTERCEPTOR solution, a connected and automated machine used for real-time thread quality monitoring.
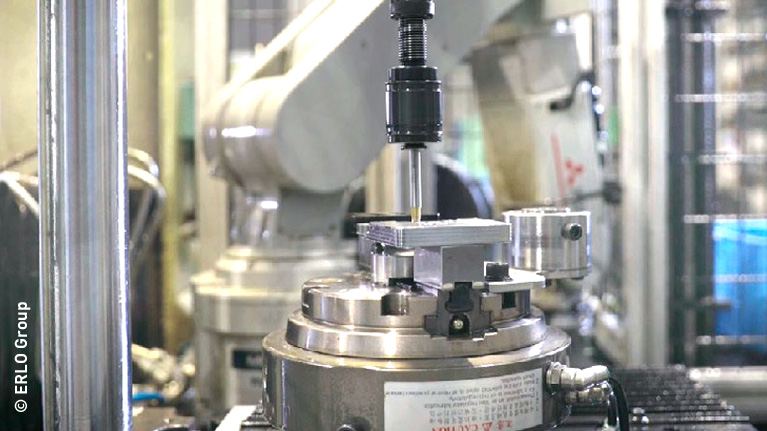
Nowadays and thanks to a number of developments reported in the industry, it is possible to monitor equipment via technologies such as Big Data to obtain real-time information on operating conditions and on any errors that may arise at a given point in time during a production cycle. This will give rise to improvements for companies in terms of equipment reliability and availability and also make it possible to measure part wear to anticipate decision-making.
It is in this context that ERLO Group, a company specialised in delivering high-productivity customised drilling and tapping solutions, has noted how crucial it is to obtain information on thread quality for customers in different sectors such as the automotive or aeronautical sectors. High-costs resulting from no-quality produced by faulty threads, on the one hand, and the lack of reliable and high-productivity thread quality verification solutions, on the other, have made it necessary to implement systems such as INTERCEPTOR. The fact that this information is available on a real-time basis and in the cloud provides early detection of worse quality threads, reduces production line costs and delivers efficiency gains, among other benefits.
Tekniker, member of the Basque Research and Technology Alliance (BRTA), is collaborating with ERLO Group in the development of a connected machine featuring technologies as Big Data to compile thread information and better manage product quality. Specifically, it is a thread-checking device that offers cloud-accessible data and provides real-time monitoring. In this manner, the machine will be able to send critical information to customers to improve the efficiency of their processes.
The technology centre is providing its know-how in terms of Industry 4.0 and connected machines to offer solutions and improvements for equipment by compiling, processing and analysing data via sensors that will make it possible to detect potential operating anomalies, perform condition diagnostics and predict possible failures.
The technological proposal is based on adapting SAM, Tekniker’s Smart Asset Management asset to store and later analyse any data received. In addition to the platform itself, it will be necessary to connect, compile and store all the information that has been compiled by means of a data logger to make it available to ERLO Group so that, in the future, machines can be included in production monitoring systems.
Innovative equipment to manage thread quality
Specifically, early detection of thread failures in production lines will not only allow Erlo but also other companies to reduce costs because an activity that until now has been done manually will be performed automatically. Additionally, and thanks to this technological proposal, production lines will gain efficiency because quality control lead times will be shortened.
It must be stressed that storage in the cloud of critical thread information will provide valuable information to allow decisions to be taken quickly. In this regard, this technology will provide companies with information on process traceability as well as relevant safety information should an incident occur. It will also be possible to discover what has caused a problem as soon as a part fails.
By implementing this project, ERLO Group will be able to enhance actions aimed at technological innovations in terms of products and services. Likewise, this machine could eventually become an outstanding tool as regards diversifying and internationalising the group’s customer portfolio.
Based on this collaboration, ERLO Group and Tekniker will set up a long-term strategic alliance to further the competitiveness of the industrial fabric to achieve further growth in the country.
Concerning ERLO Group
ERLO Group, an Azkoitia-based company, has more than 50 years of experience in the field of drilling and tapping solutions, a sector that has become an international reference over recent years. The company’s technological offer nowadays also includes the manufacture of hydraulic presses. In recent years, it has developed an extensive range of high-productivity customised drilling and tapping solutions for relevant sectors such as the automotive, energy and machine tool sectors.