Adaptable and sustainable work environments for the industry of the future
A4BLUE, the European initiative led by IK4-TEKNIKER, has developed automation mechanisms adapted to workers’ needs. A person-robot collaborative and adaptative environment has been installed at the technology centre as an Industry 4.0 pilot scenario.
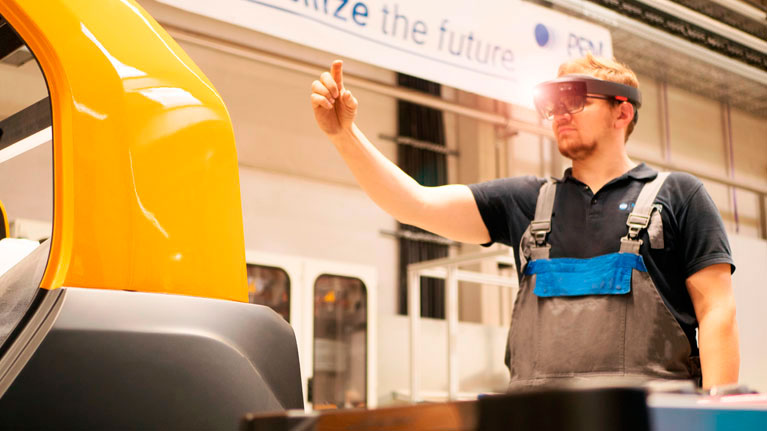
Due to strong competition in sectors such as the aeronautical business and continuous technological breakthroughs, manufacturers have been forced to increase their levels of productivity and develop highly resilient production systems.
In order to ensure that these systems actually meet workers’ needs, the team that has carried out the European A4BLUE project led by IK4-TEKNIKER has developed and validated a new generation of adaptable and sustainable workplaces to meet ever-changing process requirements and adapt them to workers’ characteristics.
This project, that started in 2016 and will conclude in September 2019, introduces adaptable automation mechanisms to perform tasks efficiently and resiliently, to provide a safe person-machine interaction as well as customised capacity-building and support for workers performing assembly work against the backdrop of augmented and virtual reality.
But adaptation does not only occur in terms of automation as it also applies to the entire workplace and intends to accommodate the needs and profiles of each worker. It is based, therefore, on an IoT (Internet of Things) architecture that provides continuous monitoring of the production context by compiling information on the different elements operating in an environment, such as, for instance, automation equipment, safety sensors, devices for interactions between individuals and automation via voice-gestures and production management systems.
A number of methodologies have been developed, moreover, within the scope of this project to determine the optimum degree of automation that a plant requires, as well as to evaluate workers’ satisfaction and the extent to which they can be used in new productive environments.
The consortium involved in the A4BLUE project has tested these new workplaces in four real environments and in which the aeronautical firms Airbus and CESA, Compañía Española de Sistemas Aeronáuticos (a division of the Héroux-Devtek group), the renowned RWTH University of Aachen and IK4-TEKNIKER itself have monitored pilot validation implementations.
Four scenarios for pilot trials
Consequently, an already existing person-robot collaborative environment has been customised at IK4-TEKNIKER’s facilities to assemble a valve used in the aeronautical sector. Fully in line with the factory’s digital transformation strategy, the technology centre has introduced a number of mechanisms to adapt the robot to workers’ characteristics plus multi-modal interaction capabilities (voice and gestures) and customised assistance to perform assembly work. In the collaborative environment, the robot also features active safety mechanisms to distinguish between inanimate objects and persons to adapt their behaviour accordingly.
In the case of Airbus, the scenario chosen has been based on the assembly of a complex hydraulic system installed on wing panels. Additionally, CESA, a leading European company that supplies fluid-mechanic equipment (currently called Héroux-Devtek Spain) has optimised the assembly of a hydraulic actuator for landing gear. Lastly, the case addressed by RWTH Aachen University has focused on improving the final stages of electric vehicle assembly processes.
This project has received funding from the European Union’s Horizon 2020 research and innovation programme under grant agreement n° 723828.