The additive manufacturing revolution finds its way into the aeronautical sector
Tekniker and Aerotecnic have collaborated in the LASTITAN project to study and optimise the manufacturing process of titanium components by using the Laser Metal Powder Deposition technique.
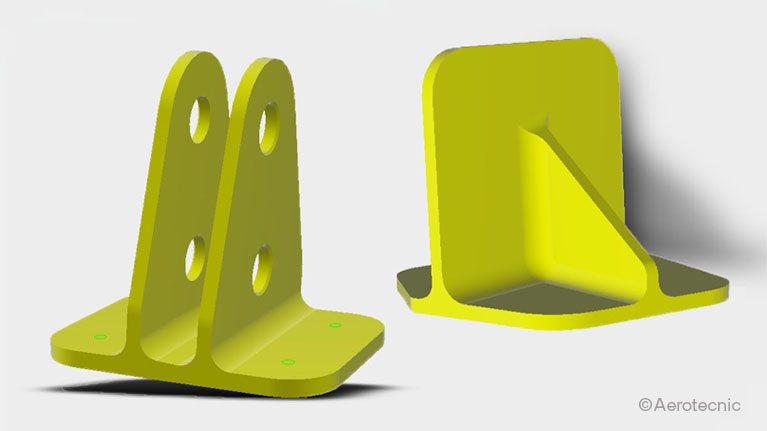
Current manufacturing processes, mainly based on subtractive manufacturing technologies (material removal processes) such as swarf removal machining are associated with significant raw material losses, even more so when dealing with structural titanium elements like those used in the aeronautical sector. Additionally, and because very expensive, high-performance alloys are used to manufacture these parts, material losses associated with the manufacturing process generate additional costs for manufacturers. Additive manufacturing technologies, therefore, represent a great opportunity for the leading companies of this industry as regards their potential to minimise the amount of material required to manufacture different types of parts or components.
The Tekniker technology centre, a member of the Basque Research and Technology Alliance (BRTA), has collaborated in LASTITAN with Aerotecnic, a manufacturer specialised in aeronautical components. The ultimate goal of this project is to study and optimise the use of an advanced manufacturing technique called Laser Metal Powder Deposition (LMD) to develop titanium components from the Aerotecnic catalogue.
This collaboration involving both industrial stakeholders will make it possible to replace the traditional manufacturing process used for different structural components based on the sector’s traditional Ti6AI4V alloy with this innovative technique that deposits several layers of metal powder injected on the surface of a given substrate which is melted by a high-power laser beam.
Based on the results obtained in LASTITAN, Tekniker intends to place itself at the forefront of the aeronautical sector and play the role of a trustworthy expert in the field of additive manufacturing techniques that represent a revolution for the aeronautical industry.
Parts with different geometries
Firstly, Tekniker and Aerotecnic chose the two parts to be manufactured within the framework of this project. The manufacturer pre-selected 12 components and the technology centre chose the two most representative items with different geometric features, one with sloping parallel walls and the other with intersecting walls. Secondly, a Tekniker robotised cell was adjusted and fitted with an inert atmosphere camera to prevent oxidation whilst parts are manufactured.
“As titanium tends to oxidise easily at high temperatures an inert atmosphere camera was installed which, when filled with argon, allows the deposition process to be caried out in an atmosphere with less than 10 parts per million of oxygen”, explains Josu Leunda, a researcher at the technology centre.
Thirdly, experimental trials were carried out on flat specimens to obtain a suitable window of parameters for the laser deposition process together and implement the most adequate deposition strategies to manufacture the define geometries.
The next stage consisted in optimising the manufacturing process for 3D geometries. In other word, small prototypes featuring the geometric characteristics of the final parts were made to adjust the strategies to each end part. These prototypes allowed Aerotecnic to run all the necessary tests to adapt the machining process to this new part typology. During this stage, deposition efficiency was also measured to quantify the amount of material lost in the form powder particles that had not been melted.
Lastly, the selected demonstrators were manufactured measuring total manufacturing process time required for both demonstrators and the resulting data was used to assess the process from a technical and economic perspective to establish comparisons with the manufacturing process currently in use.
Dimensional monitoring was also carried out on the demonstrators to check that deformation was lower than the maximum admissible level.
They were later sent to Aerotecnic to be machined under finishing conditions until the final dimensions were obtained.
Thanks to the results obtained in this project, Tekniker and Aerotecnic will be able to open up new lines of research and cooperation to learn more about how a machining process can be optimised, about the potential use of heat treatments to improve the microstructure of components and even the possibility of upgrading process efficiency and finishes.