Plasma electrolytic oxidation
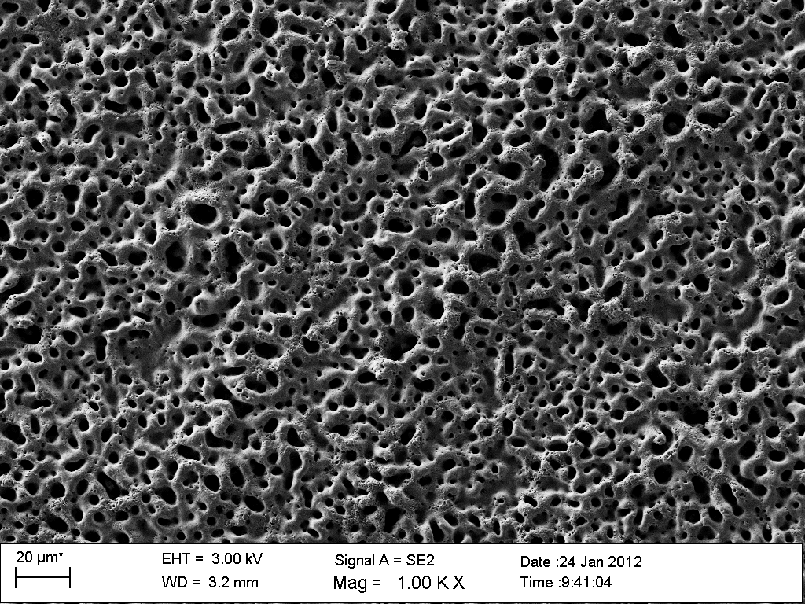
Plasma Electrolytic Oxidation (PEO) is a high voltage electrochemical process which involves generating a plasma-discharge in the metal-electrolyte interface so that the substrate surface is transformed into a hard and dense ceramic oxide layer, thus not damaging the substrate by thermal expansion. Plasma discharges occur when the voltage applied exceeds the "breakdown value" (usually several hundred volts). Today, Plasma Electrolytic Oxidation represents a rapidly growing sector of surface engineering, particularly for the treatment of Mg, Ti and Al alloys.
The PEO process is radically different from the traditional anodising process in a number of aspects. The main characteristics of the process are:
- The process employs alkaline electrolytes, the composition of which is extremely critical for the speed of coating and for the properties of the anode layer which is formed. These electrolytes are environmentally acceptable.
- The process uses alternating current at high voltage. Due to this high voltage, a micro-plasma is generated which surrounds the electrodes and the oxygen ions, produced in the plasma, are diffused through the anodic layer in the aluminium substrate, reacting and forming more anodic layers.
- Because the voltages are higher than the breakdown voltage of the layer formed, it is not necessary to have open channels to sustain the process and, therefore, thick, dense, non-porous layers can be formed.
- As the process uses controlled high voltage power, the productivity of the process is very high.
- It is not necessary to precisely maintain the bath temperature. In fact, satisfactory coatings can be obtained with variations in temperatures even up to 10-20°C, thus greatly simplifying the process.
- The electrolyte composition varies significantly for different types of coating. Depending on the type of reagents used, it is possible to vary the rate of growth of the oxide and also adulterate it with elements that give the oxide additional properties (self-lubrication, biocidal properties, etc.).
- Because of the high density of the coating, there are virtually no variations in the dimensions of the anodised part and a completely finished part can be coated without any major post-finishing operations being required. The PEO process produces a soft outer coating for about 15% which is removable by polishing or grinding so that the layer which remains is an extremely hard ceramic layer (2000Hv).