Mechatronics and precision engineering
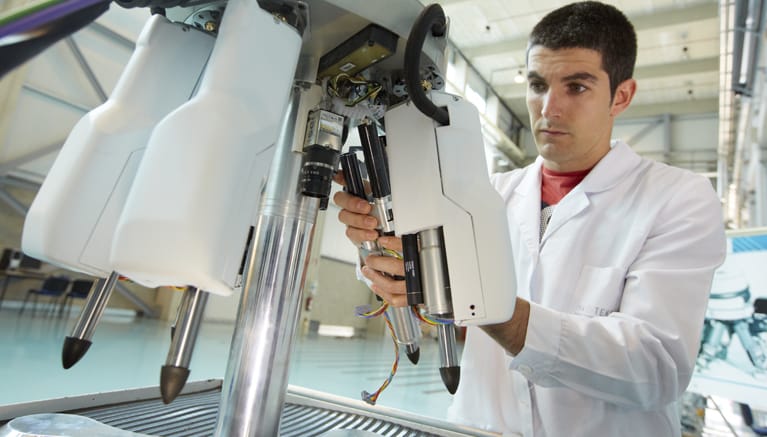
TEKNIKER works with a range of technologies enabling it to tackle the design, and the simulation and validation of mechatronic systems on the basis of needs analyses and the development of conceptual designs right up to the supply and validation of fully functional prototypes.
Mechatronics consists of synergistic interaction among various engineering disciplines (mechanics, control, micro-electronics, computing, etc.) geared towards integrating functionalities in machines or devices.
Yet the concept of precision engineering includes the design and development of machines and devices following basic principles geared towards prioritising precision over any other requirement.
The two concepts grouped together in this field of research enable TEKNIKER to excel in activities involving more basic research (for example, in magnetic levitation systems) as well as in their application, preferably through the development of prototypes in different sectors, such as machine tools, renewable energies, equipment for large scientific facilities, etc.
The technologies mastered by TEKNIKER focus not only on theoretical analyses but also on experimental results, and the correlation between the two of them is a key element for developing the most basic concept right up to the final, fully operational equipment.
The basic technologies in connection with the theoretical analyses are as follows:
- Structural analysis (deformations, stresses, fatigue, dynamics, composite materials)
- Kinematics and dynamics (multi-body systems, drive systems, driving and guiding systems, rotor dynamics)
- Precision engineering (error budget, precision design, optomechanics, compliant mechanisms, dimensional methodology)
- Fluid mechanics (hydraulics, hydrostatic and magnetorheological systems, highly-demanding pneumatics)
- Thermoenergy engineering (heat transfer, thermodynamics)
- Multi-domain and multiphysics simulation
- Temporary modelling and simulation of systems, design and controller adjustment
Work is also carried out on experimental technologies, such as:
- Stress measurement by means of extensometry
- Vibration analysis (modal , modal operational, balanced analysis)
- Temperature measuring technologies (thermography, thermocouples, pyrometry)
- Dimensional metrology by means of the development of ad hoc procedures, multilateration techniques, measuring with contact (probes) and without contact (laser, optics and inductive techniques), 3D digitization and photogrammetry.