Artificial Intelligence to optimise industrial equipment
The technology centre has applied its expertise in the areas of AI algorithmics and physical modelling by developing digital twins that can improve control fault detection and monitoring processes for industrial assets.
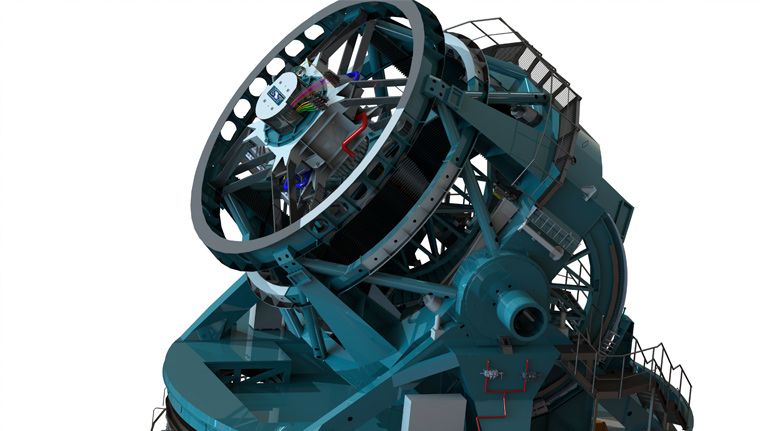
Simulation tools such as digital twins are increasingly being applied in Industry 4.0 environments to improve production process efficacy. These virtual models of equipment that allow you better understand and predict the performance features of real-life or physical equipment. They are used throughout the equipment’s entire life cycle to simulate, predict and optimise equipment operation before investing in prototypes and physical equipment.
The Tekniker technology centre, a member of the Basque Research and Technology Alliance (BRTA), has gained further insight into these technologies within the framework of the VITRUAL project in which artificial intelligence has played a key role in terms of developing models based on knowledge acquired by means of real data.
Kerman López de Calle, a Tekniker researcher, says that “thanks to AI technologies it is nowadays possible to hybridise the typologies of data-based physical models data to maximise their potential. It is also feasible, for instance, to adjust physical or complementary models to modulate physical effects or situations that are difficult to explain; or physical models can be used to recreate data that are both hard to gather and record in the industry (such as machine faults), thus facilitating the development of AI models that could not be trained without these data.”
More specifically, Tekniker has applied all of its knowhow in the areas of AI algorithmics and physical modelling to generate digital twins.
The Tekniker research centre also adds that “the twins are especially interesting whenever data covering asset faults are scarce or if equipment availability for commissioning purposes is low and the aim is to develop controls beforehand”.
Data hybridisation for diagnostics
The combination of synthetic data (i.e., data generated by physical models) with experimental data by means of AI algorithmics delivers machine fault diagnostic and detection systems that are more robust and reliable.
Hybridisation techniques of this kind are of great interest in industrial environments where assets are very costly and the aim is to prevent malfunctions. Generally speaking, and in order to prevent malfunctions, assets are subjected to continuous monitoring. Continuous monitoring also hampers the gathering of fault data required to obtain enhanced diagnostic and prognostic systems for these assets. Consequently, and thanks to the data hybridisation procedure proposed in VIRTUAL for electromechanical actuators it is now not only possible to address this problematic issue but also improve monitoring systems significantly.
Virtual commissioning
The technology centre, on the other hand, has applied what is called a virtual commissioning methodology in which virtual models are used to check equipment control software before it becomes available (connection and virtual commissioning of the equipment) in such a manner that tests are run in early project stages to detect errors in advance and reach the commissioning stage with software that is more refined.
When applied to equipment software programming, this methodology offers a large number of improvements that can summarised as follows: the amount of time required for commissioning is reduced to a minimum, risks are significantly mitigated, it become possible to run automatic tests and avoid repetitive errors, software quality is improved and software maintainability is enhanced.
Consequently, the VIRTUAL initiative has developed digital twins that allow you to test, correct and validate equipment software before having physical equipment at your disposal to fine-tune operations on real-life equipment.
Equipment optimisation
Likewise, and within the framework of this project, Tekniker has contributed, on the one hand, its knowledge in areas such as mechanics, electronics and monitoring and, on the other, in-house expertise in terms of AI algorithmics to develop models and optimise the size and design of gearboxes, speed up the design of brake-clutch control systems and components for the Large Synoptic Survey Telescope (LSST), currently under construction. Finally, the organisation has designed diagnostic systems for electromechanical actuators.
Several universities and technology centres of the Basque Country are involved in the VIRTUAL project funded by the ELKARTEK programme.