Developing a unique high-yield laser micro perforating machine
The aeronautical sector needs innovative solutions to build aircraft that is more efficient and produces less pollution.
The development of a unique high productivity industrial machine based on laser technology to manufacture micro perforated panels for vertical and horizontal tail stabilisers on commercial aircraft.
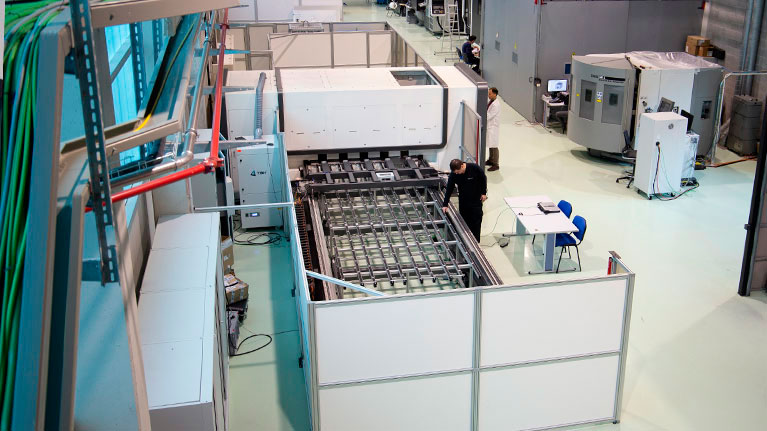
The aeronautical industry requires innovative solutions to improve aerodynamics, reduce structural weight and lessen air resistance of commercial aircraft. This would also reduce pollution and fuel consumption.
One of the most promising techniques for aircraft wings and tail stabilisers is called HLFC or Hybrid Laminar Flow Control. It is a technology that reduces aircraft resistance to air because air sucked through tiny holes.
Solutions of this kind could save up to 10% of aircraft fuel and achieve significant reductions in terms of CO2 and other polluting agents such as NOx.
The production of micro perforated metal panels for the leading edges of wings and tails, however, poses one of the most significant challenges as regards developing and implementing the HLFC technique for commercial aircraft.
It is in this context that Tekniker together with the German technology centre Bremer Institut Fur Angewandte Strahltechnik (BIAS) and Aernnova has jointly developed the first high-yield industrial laser micro drilling machine to manufacture HLFC panels.
The machine has been designed to process titanium panels measuring up to 5000 x 2000 x 0.8 mm and features productivity rates in excess of 300 drillings/second. It is also be validated at an industrial level.
It is equipped with several monitoring and control systems to ensure optimum quality of the panels to be manufactured and also provides status information on individual drillings.
Thanks to the installed laser technique, it is possible to drill holes of diferent sizes, although the standard diameter is 0.1 mm with a geometric dispersion of less than 0.005 mm.
Other supplementary processes can be performed with the machine such as cutting, marking, etc., to improve quality and facilitate subsequent manufacturing processes.
In short, the machine that has been designed is making it possible to reduce commercialisation lead times for HLFC structures and allowing for a large scale implementation of this technology in the aeronautical sector.
This project has received funding from the Clean Sky 2 Joint Undertaking under European Union´s Horizon 2020 research and innovation programme under grant agreement n° 755620.