3D vision as an assistive technology in the automotive sector to palletise parts accurately
Tekniker has developed an innovative robotic solution for Grupo Cikautxo that manipulates and moves automotive components between containers.
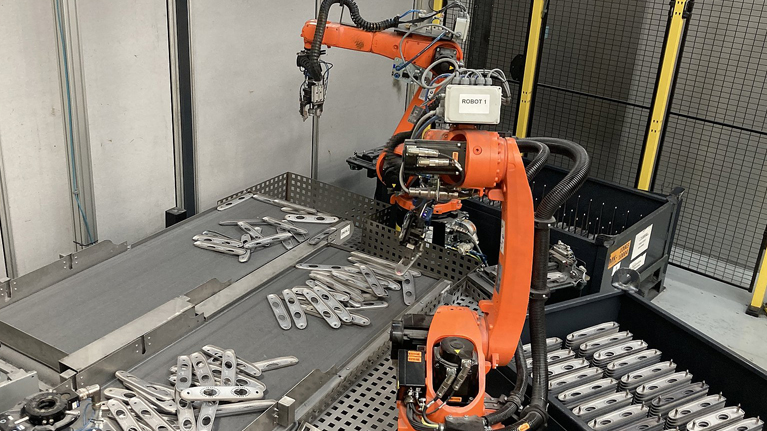
Automating palletising processes in the area of industrial production poses a major technical challenge due to the many geometric shapes involved and because of the chaotic positioning of the parts to be manipulated. The development, however, of new AI and artificial vision technologies opens up new possibilities in this field.
An example of this can be found in the innovative 3D vision system developed by the Tekniker technology centre, a member of the Basque Research and Technology Alliance (BRTA), an organisation characterised by its high degree of specialisation in providing technological solutions related to industrial robotics and automation for Grupo Cikautxo, a domestic manufacturer of automotive components.
More specifically, Tekniker’s research team has fine-tuned a robotic system controlled by artificial vision software that allows industrial components to be moved and left accurately inside containers.
The solution, that features two robots and a 3D scanner, provides a solid grip so that parts can be left inside a container specifically adapted to the features of the parts to be included in the production flow at a later stage.
Eneko Ugalde, head of Tekniker’s Smart and Autonomous systems unit underscores that “our work has focused on a vision technology called Surfaced-based Matching that operates as the robots’ eyes and helps to identify components to be moved accurately between containers at a speed of 8 seconds per unit.
Thanks to this new system developed by the technology centre it is now possible to optimise and automate a process which until now was done manually at Grupo Cikautxo. It speeds up palletisation, saves on production costs and releases workers to perform tasks that are more demanding.
Collision-free localisation
The main challenge this Tekniker configuration faces is that robots must accurately identify the position and orientation of components in 3D spaces so they can be picked up and deposited safely.
The end result is a solution based on a Tekniker asset called SMARTPICKIN that can accurately identify objects by analysing 3D data, using the surface model and entering the corresponding geometric information.
The result obtained once the analysis has been performed allows the robot to manipulate the parts in a certain order.
The asset developed by Tekniker uses HALCON libraries to manage dot clouds. These artificial vision libraries are marketed by the German engineering firm MVTec incorporated by Tekniker in 2023 as a partner fully certified to use the system.
Eneko Uglade explains that “thanks to HALCON, we can automate and optimise the entire process of robotic palletisation. The software offers a large number of sophisticated artificial vision tools that accurately locate the parts to be picked up, avoid collisions and guarantee a secure and fluid pick-and-place process”.