Smart maintenance for machine tools
The European project Power-OM has developed an innovative predictive maintenance system based on monitoring machine power consumption.
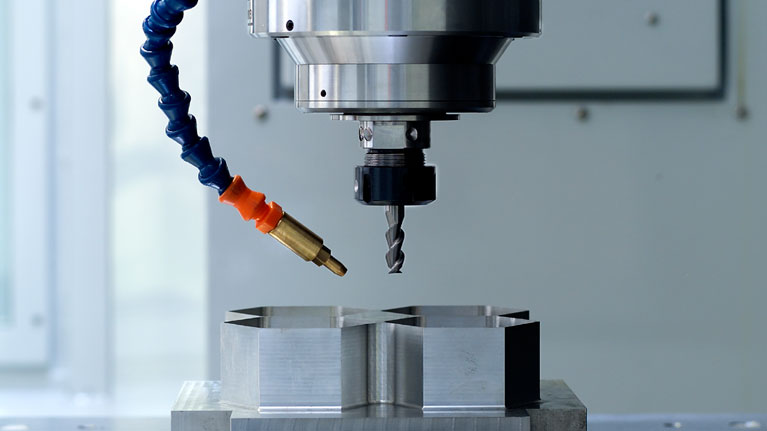
Maintenance strategies for industrial production systems usually consist in preventive practices based on prescheduled intervals complemented by reactive actions in the case of breakdowns. Machine tool users are no exception and these practices have consequences in terms of quality, cost and levels of productivity achieved.
In order to provide the industry with solutions to deal with this challenge, the European Power-OM project has developed a smart maintenance system that uses signals related to the consumption of electricity as a new way of incorporating predictive maintenance techniques and improving productivity based on three areas: optimising maintenance strategies, managing power consumption more efficiently and improving the reliability of equipment and critical components to reduce shutdowns.
Power-OM has been lead by the IK4-TEKNIKER technology centre with the participation of another two Basque companies, Goratu and Fagor Automation, a fact that clearly demonstrates the Basque Country’s leadership position as a benchmark in terms of innovations linked to the machine tool sector. Other member organisations of the consortium are Artis (Germany), Predict (France), Monition Limited (United Kingdom) and the Technical University of Lulea (Sweden).
This 3.8 million euro project, recently finished after four years of research work, has received EU funding via the 7th Framework programme.
The project’s main innovative proposal is to allow any information delivered by a machine’s numeric control to be used without having to resort to sensors.
“This novel strategy evaluates a machine’s condition by running testing cycles specifically designed to diagnose a unit’s most critical components and thus produce a machine condition report”, says Aitor Alzaga, an IK4-TEKNIKER researcher and scientific director of the Power-OM project.
Test results are generated once the processing stage has been carried out in full: a digital “footprint” of the machine, which, once cross referenced, allows the most critical components, the header and the linear guideways, to be evaluated, The project also features a cloud platform that compiles all the information obtained in order to perform comparative analyses in relation to other other machines.
It is expected that the incorporation of this machine to industrial smart maintenance actions will make it possible to reduce component failures by 75%; power consumption is to be reduced 5% and the reliability of headers and linear guideways will increase by 25%.
This project has received funding from the European Community´s Seventh Framework Programme (FP7-NMP-2012-ICT-FOF) under grant agreement no 314548.