Selective additivation of ONA dielectrics for high performance machining processes
The IK4-TEKNIKER technology centre and ONA, a machine manufacturer, are developing new solutions to enhance electroerosion machining processes (EDM) for high added value sectors such as aeronautics, wind power or the automotive business.
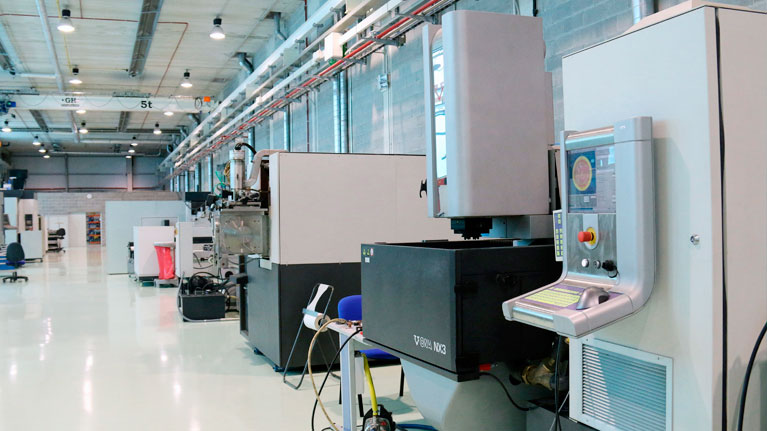
Some of he most demanding industrial sectors such as aeronautics, wind power or the automotive business require complex and high added-value components. Hardened steel and nickel and titanium alloys that achieve better performance levels and enhanced properties are currently used to manufacture components.
The specific properties of these materials, however, and their complex geometry make their processing and machining far more complex to perform when conventional machining technologies are used.
In order to overcome this problem, the IK4-TEKNIKER technology centre and ONA have joined forces in a project whose aim is to improve the efficiency of electroerosion processes whenever advanced materials are used.
“This project will help to enhance the competitiveness of manufacturing processes that use complex materials and will give a higher added value to the products offered in the machine tool market and to machining companies. These sectors are extremely important for the Basque industrial fabric and this explains why their development is a major driving force for the economy of our region”, says Marta Hernaiz, the coordinator of this initiative at the technology centre.
The project aims to improve the performance of the electroerosion process (EDM) by using advanced dielectric fluids, formulated via selective and homogeneous additivation with compounds that, thanks to their molecular structure, are able to modulate intensity and how an electrical discharge reaches the workpiece.
This system will allow parts to be made characterised by an improved surface finish and less thermal damage. It will also minimise their residual stresses and optimise mechanical behaviour. Another major advantage is that process duration is optimised, meaning that it is reduced so the user may maximise machine performance levels.
Specifically, IK4-TEKNIKER researchers will take on the responsibility of formulating the dielectrics and developing the industrial cases defined on the machine model ONA NX3.
To achieve this goal, the EDM machine has been equipped with sensors for online signal acquisition to monitor and evaluate process parameters. Likewise, and during the activity described, a characterisation is carried out covering the entire part and the electrode to fully assess the effects produced by the dielectric in terms of parameters such as process time, electrode wear and surface quality of the machined part.
Another step in electroerosion technologies
ONA is progressing by incorporating industry 4.0 technologies to its processes.
Thus, the execution of this project will allow further progress to be made in the development of electroerosion machining processes. Moreover, significant advantages will be achieved in terms of productivity improvements by reducing process duration by nearly 10%, by lessening tooling wear rates and improving the end quality of the components produced.
Additionally, the development of a new industrial EDM system in which the dielectric element will become yet another component of the machine itself represents a differential element that will make it possible to offer each customer the most suitable response as a function of their needs.
It will also help to generate more knowledge on innovative technologies such as selective additives and make it easier to transfer technological developments to the industrial sector.