Predictive maintenance to improve aircraft safety
IK4-TEKNIKER is developing new solutions for Liebherr-Aerospace Lindenberg GmbH, (Germany) to enhance the reliability of their aeronautical components.
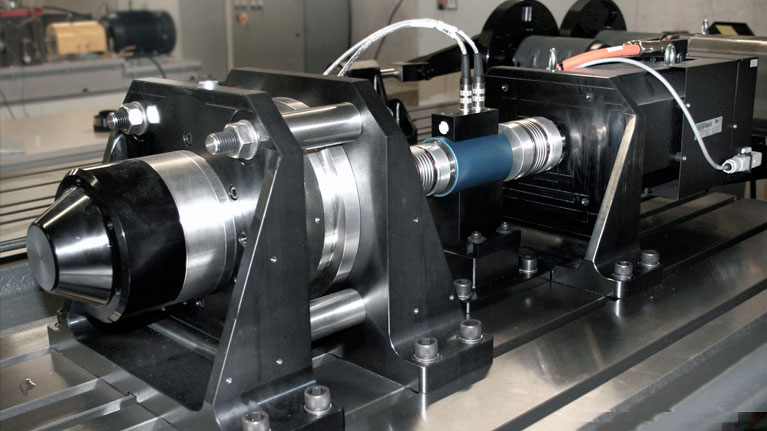
The growing trend in the aeronautical industry in terms of building lighter planes, reducing fuel consumption and lowering maintenance costs has given rise to the new concept “More electric aircraft” based on replacing traditional hydraulic and pneumatic systems by innovative electric solutions.
Multinational corporations believe that further progress must be made as regards developing new maintenance methods for electromechanical and electro-hydrostatic systems used to enhance aircraft component reliability and upgrade safety.
In order to meet these demands, IK4-TEKNIKER is currently leading a European project whose ultimate goal is to develop new predictive maintenance solutions for Liebherr-Aerospace Lindenberg GmbH, a German company that specialises in integrated systems used in the aeronautical industry. The main aim is to monitor aeronautical components and extend their life cycle.
IK4-TEKNIKER experts will study new monitoring methods for actuators used for wing control; they will also look for new alternatives to predict gear failures and carry out research actions to discover the best alternatives applicable to fuels, lubricants and gaskets to extend actuator durability. Another goal is to identify and anticipate any anomalies that might occur during aircraft operations.
This collaboration lies within the framework of the European project ISSELUB led by the Basque technology centre with the support of Liebherr-Aerospace Lindenberg GmbH as an industrial partner.
The project, that kicked off in January 2016 and will end in December 2018, has received European Commission funds totalling 680,000 euros within the framework of the Clean Sky project whose aim is to develop more sustainable aeronautical products.
Lines of research
Within the scope of the specific objectives established by ISSELUB, the technology centre will attempt to find new alternatives for aircraft component gaskets to reduce friction and wear and prevent leaking under extreme operating conditions so that life cycles can be extended.
For efficacy testing purposes, IK4-TEKNIKER has developed TESSA, an innovative test bench. It allows for the characterisation of the sealing capabilities and tribological features of a number of mechanical components throughout an extensive range of operating conditions. A climatic chamber has been designed to run tests on Liebherr actuators with temperatures ranging between -50 and +120 ºC.
The project also intends to develop new component monitoring alternatives. To do so, the technology centre has the support of a Basque company called Atten2, an IK4-TEKNIKER spin-off that develops and manufactures online optical sensors used to monitor fluids and lubricants in machines and industrial processes.
Atten2 will adapt its sensors to the fluids used in the aeronautical industry to monitor the physical and chemical parameters of lubricants flowing through aeronautical systems to spot anomalous conditions and extend component life cycles.
With a view to delivering new and efficient systems, IK4-TEKNIKER is now working on the development and implementation of an algorithm that transforms monitored data into warnings reporting critical situations. This algorithm will be able to diagnose and forecast actuator failures by delivering the information required to implement the most suitable maintenance actions and simultaneously upgrade safety and efficiency.
“We hope this project will significantly boost the European aeronautical sector”, says IK4-TEKNIKER researcher Iñaki Bravo. He also states that “our expertise in areas such as component monitoring, electronics, surface physics and chemistry, tribology and fluid sensorics allows us to make significant contributions as regards developing new predictive maintenance solutions”.