Micro-WEDM and EDM
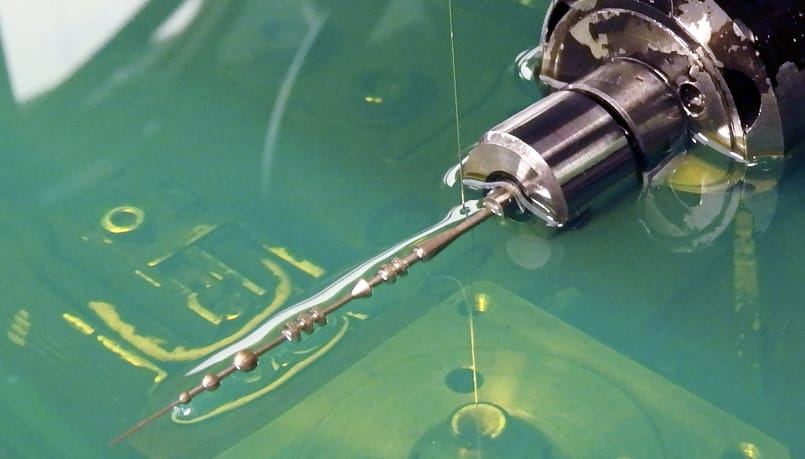
TEKNIKER develops electrical discharge machining solutions using die-sink EDM and wire electrical discharge machining.
At TEKNIKER R+D activities are being undertaken, researching into and enhancing the current process of electrical discharge machining, endeavouring to improve results and making it a more environmentally sustainable process, opening the market to a new materials and applications.
TEKNIKER’s activity in EDM uses sinker EDM and wire micro-WEDM, encompassing numerous areas: moulds, aeronautics, healthcare, microfluidics, watchmaking, wind turbine power, the automobile sector, and so on.
Both technologies enable generating complex geometries in high hardness materials with precision finishes, giving rise to the design and development of high added value products and with better performances.
EDM is a process in which machining forces are minimum, enabling the machining of materials of high hardness and/or not easily machinable ones, using other machining techniques.
At TEKNIKER the following aspects of EDM are tackled among other:
- the development of new dielectrics that enhance the rates of removal of material and the surface quality of the machined part
- the adaptation of electrical discharge machining conditions for reducing the formation of white layer and consequently the generation of residual tensions in the parts
- the introduction of external sources that assist the operation and improve the removal rates of the material
- the introduction of new dielectrics which are more environmentally friendly.
In resume, this technology encompasses:
- Micromachining using thin wires (Thin Wire EDM)
- Micro-electrical discharge machining using Oil-based Wire EDM
- Electrical discharge machining using wires of complex geometries with precision finishes and tolerances
- Assisted EDM
- New dielectrics.